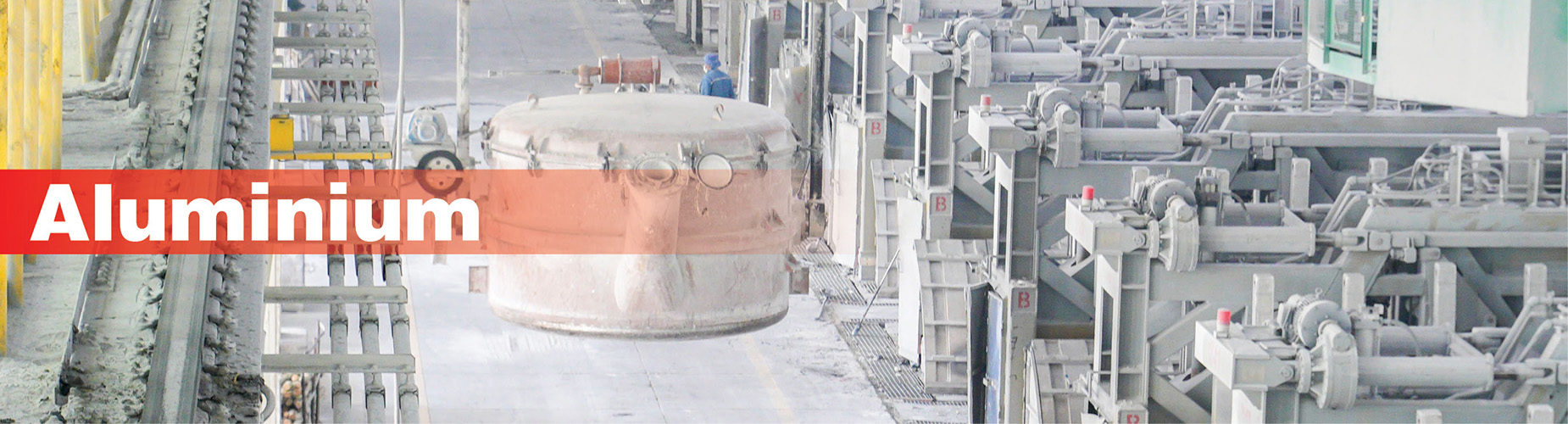
ALUMINIUM PRODUCTION
Aluminium production is a complex process with several challenging steps. High temperatures and a corrosive environment are well-known characteristics of aluminium production, aligned with the energy consumption of the electrolysis process, which operates at temperatures around 950°C. This requires large amounts of electricity, making energy one of the most significant costs..
Reducing energy loss is crucial for improving energy efficiency and lowering costs. These goals happen based on Calidit Group’s years of experience in applying the right solutions and products during the whole process of aluminium production, from the anode baking area up to casting.
It doesn’t matter whether it’s primary or secondary aluminium production; whether it is anode baking furnace, cathode plant, reduction, or casting area, by sharing your challenge with us as the one-stop high-temperature solutions provider, we will present our top-notch solutions that will be brought into the shape of a product. The solutions include thermal insulation, sealing, and protection, which cover the challenges from ABF exhaust gas suction up to molten metal protection. Our target aims to provide a solution in aluminium production, which by implementing simple or complex ideas, we are enhancing production efficiency, equipment durability and staff safety.
SOLUTIONS & PRODUCTS:
- Flexible duct (Spring joint)
- Packing
- Obturator, flue baffle
- Cover head wall
- Expansion joints
- Peep hole covers
- Cable covers
- Flexible Launder
- Protective cloth
- Launder cover
- Textile filter bag
- Thermocouple sheath
- Ceramic Filtration
- High density boards
- Siphon gasket
- Millboards
In Primary aluminium, we have lots of experiences for the following sections: